Stay Ready - So You Don’t Have to Get Ready
Discover how Transcat helps ensure long-term efficiency and compliance
A planned outage is critical to the safety and compliance of your power plant but it can also be costly. Transcat helps you manage a planned outage and maintain the safety and compliance of your power plant without sacrificing productivity with reliable, trusted support to help you.
How Transcat Helps You Manage Planned Power Plant Outages
Our customized solutions, trusted calibration services, and experienced team of experts can help your power plant ensure safe, compliant, and profitable operations – for planned outages and beyond.
Transcat can help you maintain compliance with State and Federal regulations when audited with:
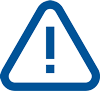
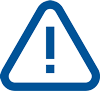
Critical Risk Assessments. Our expert critical risk assessments help ensure your plant is compliant with State and Federal regulations as well as internal regulations and processes.
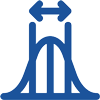
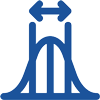
Interval Analysis. Get the right support to ensure you are compliant to internal SOP's.
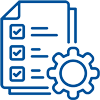
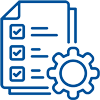
SOP Compliance. We can help you navigate SOP compliance requirements and develop a reliable plan for risk mitigation.
A critical part of plant safety and efficiency is accurate calibration of test and measurement instrumentation. Transcat is one of the world’s most trusted names in calibration and validation services. You can trust Transcat for equipment calibration and validation services, as well as reliable scheduling support to ensure you stay ready, so you don’t have to get ready.
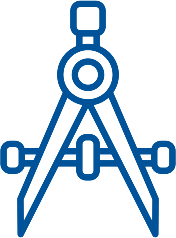
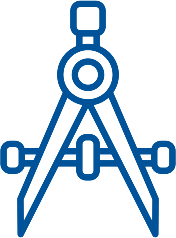
Scheduled Calibration Maintenance
Our team will develop a scheduled calibration maintenance program that is specific to your needs and goals without requiring a bi-yearly shutdown. Our expert technicians can even deliver your services directly on site at your power plant.
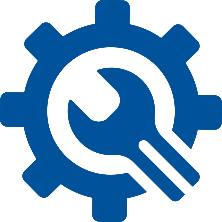
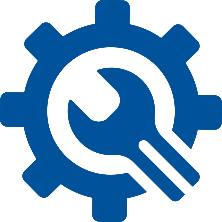
Planned Shutdown Maintenance
This full-service offering gives you the support of an onsite shutdown coordinator as well as access to our full scope of project management services strategically customized to the needs of your organization.
PM Planning. Transcat can develop reliable preventative maintenance (PM) scheduling to suit your needs, as well as providing on-hand inventory levelling.
On-Hand Inventory Planning. Our team will help you manage stock levels to meet demand efficiently, while our Rentals and Distribution teams can support spare part needs - as per operation/equipment class.
PM Mobilization and Scheduling. Trust Transcat to effectively organize and schedule preventive maintenance activities in order to minimize downtime and costs.
Our experienced team can manage your project from start to finish, supporting you with:
✔ A consultation and comprehensive project plan
✔ A custom-tailored equipment management program that includes calibration services, testing procurement, asset management and more based on
✔ Tiered support structure based on your requirements – dedicated program management team to coordinate all equipment needs or segmented support, working with existing third-party vendors
Criticality Assessment. Our team will evaluate your equipment criticality and help you create a strategy to minimize the impact of equipment failures.
Asset Hierarchy Development. We will classify your equipment by hierarchy in order to analyze potential failure impacts across multiple systems.
Predictive Maintenance Planning (PdM). Experts will assess equipment data to develop predictive maintenance schedules in order to prevent potential equipment failures - ensuring fit-for-purpose and reducing potential downtime.
FMECA/RCA. We also have the capacity to analyze failures in order to identify their root causes and failure impacts.
Business Intelligence. Our experts can analyze your data and help you use it to support strategic business decisions.
Setting & Reporting Key Performance Indicators. Together we can identify the key metrics that will help you effectively measure performance and outcomes.
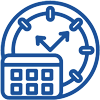
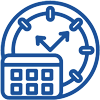
Timeline & Consulting Support. Our team will support you in developing planned shutdown timelines and provide other consultative recommendations.
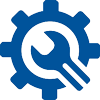
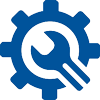
Maximized Maintenance Plans. Not all maintenance requires a shutdown. Transcat can help you determine the right maintenance at the right time.
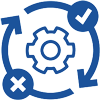
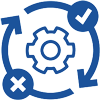
Testing Support. Ancillary to your maintenance services, we can also provide testing support to ensure safety and efficacy of your equipment and processes.
Make Your Next Outage Your Most Efficient – and Effective - Yet
Our team has extensive experience supporting power plants like yours through both planned and unplanned outages. Here’s why you can trust Transcat to help you prepare for your next outage:
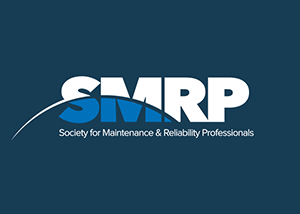
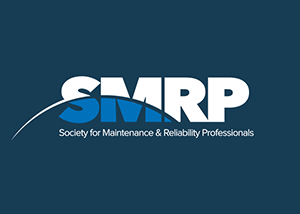
Aligned with SMRP on maintenance and reliability best practices
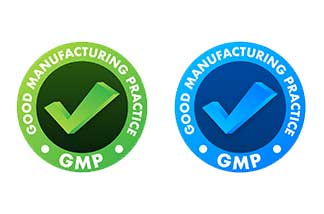
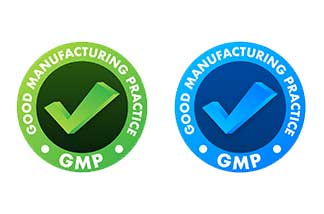
We apply Good Manufacturing Practices to ensure compliance with regulatory expectations


In mechanical and process engineering projects, we adhere to ASME and API standards
Other quality control practices include:
✓ ISO 55000 Asset Management
✓ ISO 9001 Quality Management Systems
✓ ISO 31000 Risk Management
✓ ISO 45001 Occupational Health and Safety
✓ 17025 – The international standard that sets requirements for the competence and consistent operation of testing and calibration laboratories
Trust Your Power Plant Maintenance to Transcat
Some of the world’s largest life science and medical device companies trust Transcat to help them safely and efficiently manage planned outages - investing more than $6M with Transcat this year.
Contact Transcat for Your Planned Outage Needs
Find out how Transcat can support your plant maintenance and safety. Connect with our team today.