
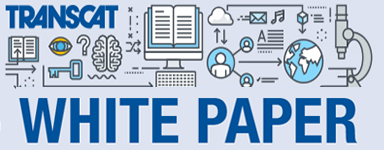
Traceability
We forgot the customer!
Everyone in the field of metrology talks about traceability, what it means and how it relates to the calibrations they perform. How often do metrology labs talk about how it affects the customers? The customer is left to figure out what traceability means with little guidance from the people who are supposed to understand it the best, the metrology labs. Sure, there are papers that discuss traceability and many FAQ pages that attempt to help the customer understand the link to them.
It’s understandable how the customer might be confused. We in the metrology field shouldn’t be surprised by the fact that a customer doesn’t understand what it means to be traceable to NIST especially since the phrases, “traceable to NIST” and “NIST traceable” are so deeply rooted in the US measurement community history. It isn’t a surprise when customers request copies of all the certs for all the assets used on their calibration because that is what they think is needed to show traceability even though the calibration lab may be accredited. We shouldn’t be surprised when customer’s look to us to help them understand.
In this paper, I will attempt to explain how the customer’s traceability is linked through the metrology lab process allowing the customer to understand how the traceability chain works and affects their process or product.
Introduction
Most users of Test and Measurement Equipment (T&ME) don’t fully understand traceability. Many times it is not the users of T&ME calling asking for the calibration, it is a purchasing agent. More often than not customers ask for their calibration to be “traceable to NIST” or “NIST traceable”, neither of which can be achieved, even NIST says so. Some customers even ask for NIST numbers or NIST traceability numbers, but these too aren’t correct unless they are getting the calibration directly from NIST. The VIM [1] (the metrology world dictionary) refers to this as Metrological Traceability. It isn’t necessarily any particular groups’ fault that a clear and concise understanding hasn’t been thoroughly explained to our customers. It is much easier to go with the flow and continue to use the phrases. The customers are requesting what they always have and the metrology community, knowing what they mean, continues to provide them information that satisfies them although incorrectly identifies the traceability. This process doesn’t help our customers or the metrology community in the long term.
Metrological Traceability
I think to understand where the metrology world left the customers behind we have to delve into the definition of metrological traceability.
Metrological Traceability: property of a measurement result whereby the result can be related to a reference through a documented unbroken chain of calibrations, each contributing to the measurement uncertainty. [1]
So let’s start with the very first part of the definition, “property of a measurement result...” So what does this mean? It means that traceability applies to the measurements and therefore you cannot be traceable to NIST. NIST is an organization, a National Metrology Institute or NMI, who makes measurements with associated uncertainties. NIST is part of the traceability chain and so you can be traceable through NIST measurements but not to the organization. We link traceability from the measurements made on the customer’s instrument to the measurements of the standard used to calibrate them. So we are clear on what calibration is, the VIM definition is below.
Calibration: operation that, under specified conditions, in a first step, establishes a relation between the quantity values with measurement uncertainties provided by measurement standards and corresponding indications with associated measurement uncertainties and, in a second step, uses this information to establish a relation for obtaining a measurement result from an indication.[1]
Notice the definition of calibration states nothing about adjusting the device under test (DUT). It is strictly the comparison of the DUT indications to the standards value.
So back to our definition of metrological traceability. We know that it is the “property of a measurement result” but the next part I think is the most important to this paper and the understanding of traceability, “…whereby the result can be related to a reference through a documented unbroken chain of calibrations, each contributing to the measurement uncertainty.” Notice that in the definitions of calibration and metrological traceability that measurement uncertainty is a key component. The measurement uncertainty is the link that binds the unbroken chain of calibrations, like the weld of each link. Based on the definitions of calibration and metrological traceability you can’t have traceability without the measurement uncertainty. The measurement uncertainty can be stated in various ways but it is still essential.
The next logical question to ask is, what are we trying to be traceable to then? Where does the unbroken chain end? The ideal ending of the traceability chain is the International System of Units (SI). There are 7 base units. NIST and other NMIs are only part of those chains. See the simple illustration below of a typical handheld digital multimeter (DMM) traceability chain. A typical handheld DMM has several functions including DC and AC volts, DC and AC current, frequency, temperature. Every measurement made during a calibration has a path for traceability back to one or more of the seven SI units.
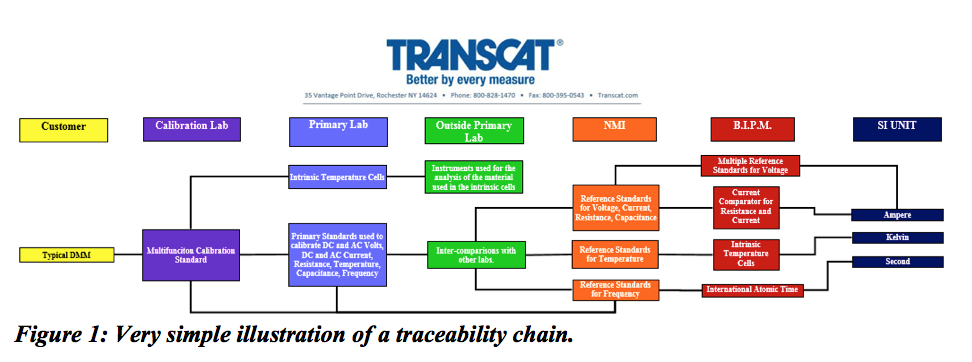
The Customer
If you have made it this far without falling asleep, you’re likely realizing that all that has been done is to restate definitions and not explain how this helps the customer relate the measurements they make on their systems or products back to metrological traceability. Your second thought might be that the illustration in Figure 1 is oversimplified. You are correct. The traceability tree for even a simple DMM could be many times more complicated if it showed every possible path.
So let’s help the customer. Let’s use an example to follow the traceability of a seemingly simple device like a digital caliper used to measure a 1 inch part in a customer product. The traceability chain starts way back at the SI unit of length, the meter. The meter (m) has been defined in terms of a constant of nature: the length of the path traveled by the light in vacuum during a time interval of 1/299,792,458 of a second. It is the responsibility of NMIs to realize the SI units and disseminate the traceability to the SI via calibrations with associated uncertainties.
NIST realizes the meter using a laser as would most all other NMIs. NIST does this per the requirements of the BIPM (Bureau International des Poids et Mesures in France) and does inter-comparisons with other NMIs to ensure their realization and uncertainty corresponds with other NMIs. This comparison allows all the NMIs to agree on what the realization of the meter should be within their associated uncertainties. This means they don’t all come up with the same number. They all might have slightly different numbers but they all agree with their respective uncertainties. Let’s say our NMI has determined they have the ability to measure a 1 inch master gage block with an uncertainty of ±0.001 µinch, this is not a factual number just one made up for ease of following math and traceability chain. This is the first link of our traceability chain back to the SI unit.
The gage block calibrated by our NMI for the Primary (Reference) Lab has a specific value and associated uncertainty when used. The associated uncertainty is a combination of many factors (including the NMI uncertainty, that is the link in our chain) that would contribute to the error in the use of the master gage block to calibrate a working gage block.
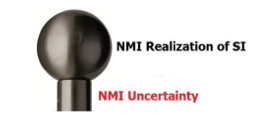
The Primary Lab uncertainty includes the uncertainty of the NMI as part of the Primary Labs uncertainty. The calibration of the working gage block was performed by a Primary Lab that has an uncertainty of ±0.1 µinch.
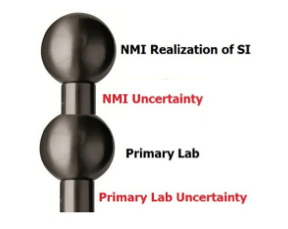
We are making our way back to the customer. We have now linked to the SI unit through our NMI down to the Calibration Lab. The working gage block has an uncertainty when it is used which includes the uncertainty of the Primary Lab and subsequently our NMI. The calibration lab has an uncertainty at 1 inch of ±10 µinch. The uncertainty for the calibration lab includes the uncertainty of the Primary Lab. The calibration lab calibrates the customer’s caliper using the 1 inch working gage block.
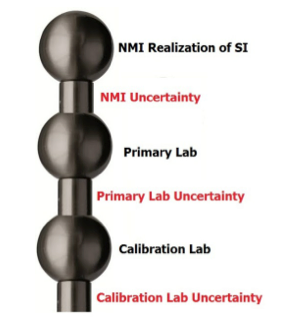
The caliper is used to check the customer’s part. The customer would need to determine the uncertainty for using the caliper to check the part. In the determination of the customer’s uncertainty, they would include the Calibration Lab’s uncertainty. The Calibration Lab’s uncertainty includes the Primary Lab’s uncertainty which included the NMI uncertainty. This is how we link traceability from one measurement to the next all the way to the customer product whatever that may be.
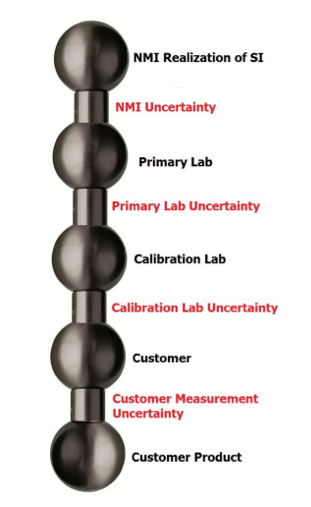
Conclusion
The traceability chain is linked to the SI units via the measurements and their associated uncertainties not back to an organization like NIST. Accreditation of a lab to ISO17025 is a way of showing the labs measurements are traceable to the SI units. Since the lab is required to know its uncertainties and include them in the measurements it makes it is effectively including the links of the traceability chain in every measurement. It is in the customer’s best interest to ensure that they understand the traceability chain. When the customer asks the calibration lab for a calibration on their equipment they need to know the uncertainties of those measurements. This will allow them to know they have traceability.
References
1. JCGM, International Vocabulary of Metrology – Basic and general concepts and associated terms (VIM), 3rd Edition, 2012.
About the Speaker
Jeremy Sims is the Quality Manager for Transcat, Inc. He received his metrology training in the U.S. Navy in Biloxi, MS in 1997. Jeremy continued his Navy career at Naval Air Station North Island in San Diego, CA. From there, he moved to Austin, TX in 2000 where he worked for Ion Implant Services as a machine technician/operator. Jeremy joined Transcat as a Calibration Technician in St. Louis, MO in 2001 before accepting his appointment to Quality Analyst in 2005. In 2013, Jeremy accepted his appointment to the position of Quality Manager for Transcat. Jeremy has earned his A.S. in Engineering Science from Monroe Community College. He has plans to pursue his B.S. degree in Electrical Engineering.
Transcat, Inc. is a leading provider of accredited calibration, repair, inspection and compliance services, including analytical instrument qualifications, equipment and process validation. Targeted industries include life science, biotechnology, medical device, pharmaceutical and other FDA-regulated industries, industrial manufacturing, energy and utilities, chemical manufacturing and other industries. Throughout its 18 strategically located centers of excellence in the United States, Canada and Puerto Rico, Transcat delivers precise services with reliable turn-around times. The breadth and depth of measurement parameters addressed by Transcat’s ISO/IEC 17025 scopes of accreditation are believed to be among the best in the industry.
In addition, Transcat operates as a leading distributor of professional grade handheld test, measurement and control instrumentation. Through its distribution products segment, Transcat markets and distributes premier and propriety brand instruments to nearly 15,000 customers. The Company offers access to more than 25,000 test, measurement and control products. Transcat’s growth strategy is to expand its product and service platform, comprised of a balanced suite of test products and analytical, calibration, compliance, and validation services. The goal is to deliver specialized technical services with a quality assurance approach, which maximizes document accuracy and on-time job delivery. Transcat answers the call with cGMP, GLP, and GXP compliant services. Transcat can provide life science companies with a reliable alternative service and product solution to the OEMs and to the “generalist” service providers who cannot meet the client’s specialized needs.